Starting at the end of 2015 six new North American propane dehydrogenation (PDH) plants are expected to come online. These new plants will have the capacity to convert up to 170 Mb/d of propane into much more valuable propylene. If all the plants are built, these new supplies of propylene should more than replace declining output from olefin crackers and refineries. These on-purpose PDH plants should also make propylene supply more directly responsive to feedstock prices. Today we describe how PDH plants are likely to impact the propane market.
We last posted a blog about propylene just over a year ago (see Oh Propylene – Why Can’t You be True?). As we explained then, propylene (C3H6 - also known as propene) is chemically similar to propane (C3H8) – it just has two less hydrogen atoms. Without those two hydrogen atoms, the propylene molecule is significantly more reactive than propane, making it an ideal chemical building block. Propylene is used in downstream petrochemical processes to make films, packaging and synthetic fibers. About two thirds of propylene is used to make polypropylene - one of the best-selling plastics, second only to polyethylene. Polypropylene is used extensively in automobiles and in the manufacture of packaging films, bottle caps, fiber ropes as well as bicycle helmets and disposable diapers. According to IHS, the world consumed about 90 million metric tons per annum (mtpa) or 198 billion pounds of propylene in 2013 - expected to increase to 130 mmtpa (286 billion pounds) within the next decade. Current US demand is about 14 billion pounds per year. China is expected to drive propylene demand, which is tied closely to economic growth.
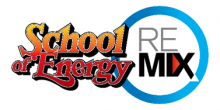
It's a REMIX!
RBN's School of Energy has been reworked, restructured and reorganized to make the conference even better - more content, more models and more labs.
Houston - October 29-31, 2014
Calgary - March 30 - April 1, 2015
Propylene is primarily manufactured today as a byproduct of other industrial processes, the most significant being petrochemical steam cracking and refinery catalytic cracking. Steam crackers produce “polymer grade” propylene in various quantities as a byproduct - depending on the feedstock used. Heavier feedstocks such as naphtha produce a higher percentage yield of propylene (about 17 percent) than lighter feedstocks such as ethane (about 3 percent). [Note: on Monday September 22, 2014 we publish our latest Drill Down report for Backstage Pass subscribers - detailing how the economics of olefin steam crackers depend on the feedstock used and the byproducts produced along with ethylene – including propylene.] Oil refineries produce propylene as a byproduct of fluid cat cracking (FCC) units. FCC units are primarily used to produce gasoline-blending components from light vacuum gasoil (see Going to a VGO). Outputs from the FCC unit are input to a propylene splitter to produce “refinery grade” propylene. A big challenge for the petrochemical industry is that both of these byproduct processes are producing less propylene for two reasons. First because gasoline production from refineries is declining with US demand for that fuel and FCC throughput is down as a result (see No Apparent Demand). Second olefin steam crackers are increasingly using ethane as a feedstock because the shale gas revolution has made it cheap and abundant. Using ethane instead of heavier feedstocks (like propane or naphtha) reduces the by-product output of propylene.
Join Backstage Pass to Read Full Article